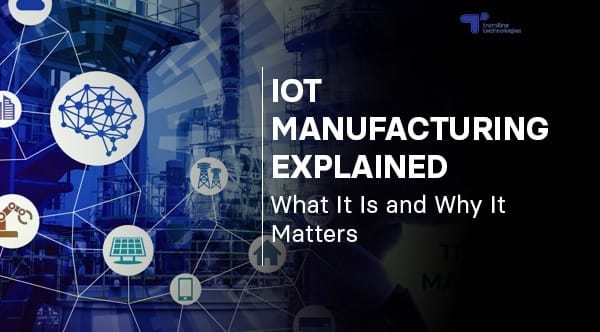
Manufacturing facilities worldwide are discovering how Internet of Things (IoT) manufacturing can solve everyday operational challenges. While the term might sound technical, IoT in manufacturing simply means connecting machines and systems to gather useful data that helps make better decisions on the factory floor.
This approach has gained significant traction as manufacturers face increasing pressure to improve efficiency and reduce costs while maintaining product quality.
Understanding IoT in Manufacturing Industry
The core of manufacturing IoT lies in its practical applications. Picture a typical factory floor where machines run until they break down, quality checks happen manually, and energy usage goes unmonitored.
IoT solutions for manufacturing change this approach by adding sensors and monitoring systems that provide real insights into operations. Transline's Intelligent IOT Solutions exemplify this evolution, helping factory managers spot potential issues before they become costly problems.
A metal fabrication plant in Detroit recently installed IoT sensors across their cutting machines. Within three months, they identified patterns in tool wear that allowed them to optimize replacement schedules, reducing downtime by 40%. This kind of practical application shows how IoT in manufacturing industry creates immediate, measurable benefits.
Key Applications and Benefits
Smart Monitoring and Maintenance
- Machine sensors detect when equipment needs maintenance based on actual usage rather than calendar schedules. This Internet of Things manufacturing approach typically cuts unexpected breakdowns by more than half. A recent automotive manufacturer found that after installing smart monitoring systems, they reduced maintenance costs by 30% in their first year.
- The real power of IoT monitoring comes from its ability to learn and adapt. For example, Transline's sensor systems can identify subtle changes in machine vibration patterns, often indicating potential failures weeks before they occur. This predictive capability allows maintenance teams to schedule repairs during planned downtime, dramatically reducing production interruptions.
Enhanced Quality Control
- Traditional methods rely heavily on random sampling and human inspection. Modern IoT solutions for manufacturing use advanced cameras and sensors, along with AI-powered surveillance to check every product coming off the line. This comprehensive inspection catches problems early, reducing waste and ensuring consistent quality.
- A food packaging company implemented IoT-based quality control and saw defect rates drop by 45% within six months. The system not only identified defective products but also helped pinpoint the root causes of quality issues, leading to process improvements that enhanced overall production efficiency.
Supply Chain Visibility
- Manufacturing IoT extends beyond the factory walls. Sensors track inventory levels and movement in real time, helping factories optimize stock without shortages. With Transline's CCTV surveillance integrated into these systems, managers gain visual oversight of their entire operation.
- One electronics manufacturer used IoT sensors to track component inventory and production rates. The system automatically adjusted order quantities based on actual usage and lead times, reducing inventory costs by 28% while eliminating stockouts. This level of automation demonstrates how IoT solutions for manufacturing can streamline complex supply chain operations.
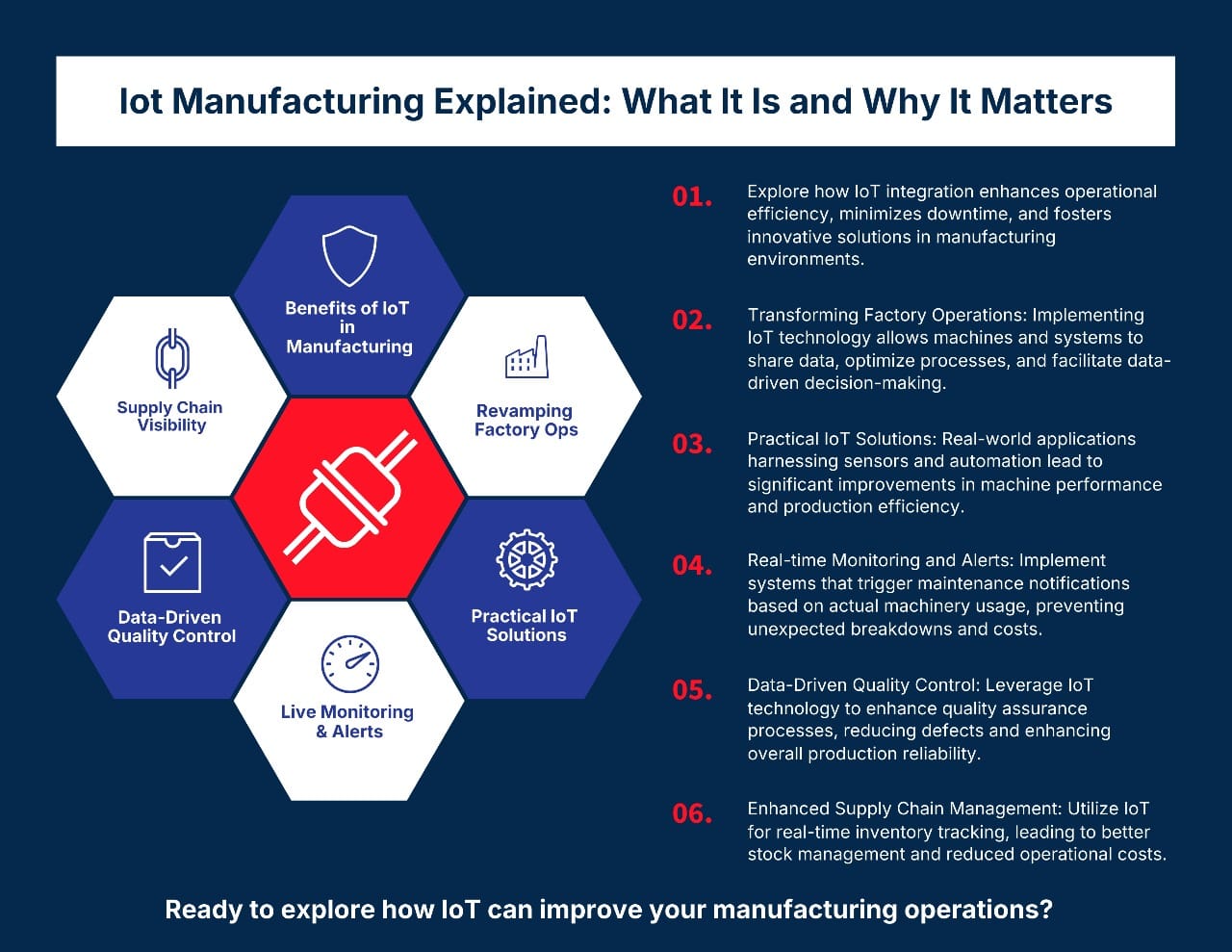
Real-World Impact of IoT Solutions for Manufacturing
The practical benefits of IoT in manufacturing industry show up clearly in operational metrics:
Equipment downtime reduced by 35%
Maintenance costs cut by 25-30%
Energy consumption lowered by 20%
Quality defects decreased by 40%
Inventory carrying costs reduced by 28%
Production efficiency improved by 25%
Labor productivity increased by 20%
These improvements directly affect the bottom line, making manufacturing IoT investments worthwhile for companies of all sizes.
A medium-sized plastic injection molding facility reported a complete return on their IoT investment within 14 months, primarily through reduced scrap rates and improved energy efficiency.
Implementation Considerations
Bringing IoT manufacturing solutions into existing operations requires careful planning. Security stands as a major priority - connecting systems to networks demands robust protection. Transline Technologies, with 24 years of expertise in industrial technology, builds security into every layer of their IoT implementations.
A multi-layered security approach includes:
Encrypted data transmission
Secure access controls
Regular security audits
Automated threat detection
Secure firmware updates
Physical security measures
Data management presents another key consideration. IoT in manufacturing generates substantial information that needs proper handling.
Transline's integrated solutions combine smart sensors with intuitive monitoring interfaces, making it easier for operators to spot trends and respond quickly to issues.
Practical Steps for Getting Started
Assessment and Planning
Start by identifying specific operational challenges that IoT manufacturing could address. Common starting points include:
Equipment monitoring for reduced downtime
Quality control improvements
Energy usage optimization
Inventory management enhancement
Production line efficiency
Worker safety monitoring
Environmental compliance
Implementation Strategy
Begin with targeted solutions that address your most pressing needs. Transline's modular approach to IoT solutions for manufacturing allows companies to start small and expand based on results. This measured approach helps manage costs while demonstrating value.
A phased implementation typically follows this pattern:
- Initial pilot program on critical equipment
- Data collection and analysis phase
- Process optimization based on insights
- Expansion to additional areas
- Integration with existing systems
- Continuous improvement and scaling
Staff Training and Support
Success with Internet of Things manufacturing depends on proper training and support. Ensure operators understand how to use new systems effectively. Most workers find their jobs become more productive once they adjust to IoT-enabled tools and processes.
Transline provides comprehensive training programs that cover:
- Basic system operation
- Data interpretation
- Troubleshooting procedures
- Security protocols
- Emergency response
- Best practices for daily use
Cost Considerations and ROI
While implementing IoT in manufacturing industry requires investment, returns typically justify the expense. Most manufacturers recover costs within 12-18 months through:
Reduced equipment downtime
Lower maintenance expenses
Improved quality control
Better energy efficiency
Optimized inventory levels
Increased productivity
Enhanced customer satisfaction
Regulatory Compliance and Reporting
- Manufacturing facilities face growing pressure to meet environmental and safety regulations. IoT manufacturing systems simplify compliance by automatically collecting and documenting required data. For example, a chemical processing plant uses Transline's sensor networks to monitor emissions and water usage in real-time.
- The system automatically generates compliance reports and alerts operators if readings approach regulatory limits. This automated approach not only ensures compliance but also reduces the administrative burden on staff.
- The plant's environmental compliance team estimates they save 15-20 hours per week on documentation while maintaining more accurate records.
Worker Safety and Environmental Monitoring
- IoT solutions for manufacturing have proven particularly valuable for worker safety applications. Sensors can monitor environmental conditions like air quality, temperature, and noise levels, alerting supervisors to potential hazards before they affect workers.
- A large automotive parts manufacturer installed Transline's integrated monitoring system to track both machine performance and workplace conditions.
- The system includes wearable devices that alert workers to dangerous situations and help maintain safe distances from operating machinery. Since implementing these IoT manufacturing safety measures, the facility has seen workplace incidents drop by 65% and insurance premiums decrease by 28%.
Cost-Effective Scaling Strategies
- Many manufacturers find success by starting with focused implementations in high-impact areas. A textile manufacturer in Gujarat began with IoT sensors on their most critical spinning machines.
- After seeing a 40% reduction in unexpected downtime, they gradually expanded the system across their entire facility. This measured approach allowed them to manage costs while building confidence in the technology among workers and management alike.
- The success of this scaling strategy has inspired other manufacturers to follow suit. A medium-sized auto parts manufacturer adopted a similar approach, starting with their precision machining department. They installed sensors on five CNC machines initially, focusing on vibration analysis and temperature monitoring.
Within four months, they prevented three major breakdowns and saved approximately ₹15 lakhs in potential repair costs. This proof of concept led to facility-wide implementation across their 50-machine operation.
Advanced Analytics and Decision Support
- Modern IoT manufacturing systems go beyond simple monitoring to provide sophisticated analytics support. These systems analyze patterns across multiple data points to suggest optimal operating conditions.
- An automotive parts supplier uses this capability to automatically adjust machine settings based on material properties, temperature, and production speed. This smart optimization has led to a 30% reduction in defects and a 25% increase in throughput.
- The power of advanced analytics becomes even more apparent in complex manufacturing environments. A pharmaceutical manufacturer implemented pattern recognition algorithms to monitor their sterile manufacturing process. The system analyzes over 100 variables simultaneously, from air particle counts to operator movements.
This comprehensive analysis helped them identify previously unknown factors affecting product quality, resulting in a 45% reduction in batch rejections and saving over ₹2 crore annually in lost production costs.
Remote Monitoring and Management
- The ability to monitor and manage operations remotely has become increasingly valuable. Plant managers can now oversee multiple facilities from a central location, making quick decisions based on real-time data.
- A food processing company with facilities across three states reduced their management overhead by 35% while improving response times to production issues by implementing centralized IoT monitoring.
- This remote capability proved particularly valuable during unexpected disruptions. When travel restrictions affected their operations, a large chemical manufacturer maintained productivity by managing their plants remotely. Their IoT system enabled engineers to diagnose and resolve equipment issues from afar, reducing the need for on-site visits by 70%.
The remote monitoring system also helped them optimize shift schedules and maintain quality standards across all locations, resulting in a 25% improvement in overall equipment effectiveness.
Integration with Business Systems
- IoT manufacturing solutions work best when integrated with existing business systems. By connecting IoT data with ERP and scheduling systems, manufacturers gain a complete view of their operations.
- A metal fabrication company integrated their IoT sensors with their ordering system, automatically triggering material purchases based on actual usage patterns.
- This integration reduced stockouts by 60% while keeping inventory carrying costs at optimal levels. The benefits of system integration extend throughout the supply chain. A large electronics manufacturer connected their IoT production monitoring with their customer order management system.
This integration enabled real-time production adjustments based on actual order flow, reducing finished goods inventory by 40%.
The system also automatically updates customers about order progress, leading to a 50% reduction in status inquiry calls and improved customer satisfaction scores. Their success demonstrates how integrated IoT systems can improve both operational efficiency and customer service simultaneously.
Moving Forward with Manufacturing IoT
- Small and medium-sized manufacturers often question if IoT for manufacturing suits their operations. The answer increasingly points to yes, especially with flexible solutions now available.
- Transline's approach allows companies to begin with crucial needs - whether equipment monitoring, quality control, or security - and grow systematically.
- Success with IoT manufacturing depends largely on choosing the right partner. Look for providers with proven industrial experience and ongoing support capabilities.
Transline Technologies combines manufacturing expertise with advanced IoT solutions, helping companies navigate the transition to connected operations smoothly.
Take the Next Step
Ready to explore how IoT can improve your manufacturing operations? Get in touch with our team to explore how our Intelligent IoT Solutions can transform your manufacturing business. Our team will assess your specific needs and recommend practical solutions that deliver measurable results.
For more information about implementing IoT solutions in your facility, reach out to our technical team. We'll help you identify the best starting point for your IoT manufacturing journey and develop a plan.